Digital Operations Platform: A New Approach to Manufacturing Employee Retention and Operational Success

Retaining key talent is a top business challenge for the nation’s manufacturing companies, according to Deloitte’s 2023 Manufacturing Industry Outlook. One-third of the manufacturing executives surveyed named retention of high-performing employees as their strategic priority for this year.
This pressing workforce challenge – which is intensified by the fact that employees departing by choice outnumbers layoffs and terminations, according to the Deloitte study – reduces manufacturing organizations’ operational efficiencies and profit margins.
Manufacturers that make improvements to employee experience, however, will better retain top talent, thus driving quality output and profit generation. A Harvard Business Review study released in 2022 showed that companies that perform well on employee experience also achieve higher levels of customer satisfaction, which then translates to positive business outcomes. A Gallup report provided further specifics, indicating that employee engagement levels in top- and bottom-quartile business units and teams represented a 64% difference in safety incidents, a 41% difference in product quality and an 18% variance in productivity – all areas that directly tie to profits.
What this underscores is that employees are the most important determinant of organizational success. Performance and productivity are enhanced when employees feel heard and cared about, are engaged in the company’s mission and have consistent opportunities to learn and grow. The impact of that positive employee experience is made visible through a digital operations platform (DOP) approach.
CONNECTING THE EMPLOYEE EXPERIENCE TO OPERATIONS
DOP, a term coined by Forrester Research and adapted by AEM member and technology advisor Net at Work, provides data visibility across the manufacturing organization through best-of-breed, next-generation systems integration to help identify trends, relationships and root causes that may be tied to the employee experience. For example, by connecting the employee record to quality and production output, manufacturers can pinpoint current employee sentiment and implement training and development opportunities that enhance engagement to better achieve optimal results.
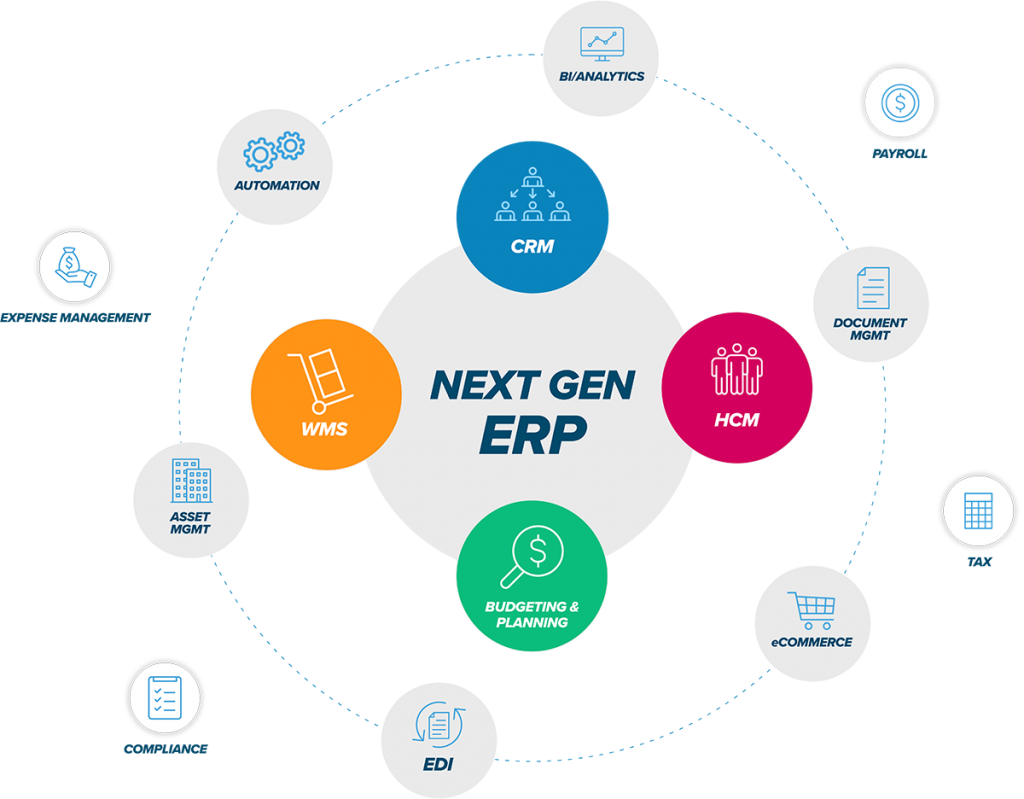
A sample manufacturing DOP, with next-generation Enterprise Resource Planning (ERP), like Sage X3, and Human Capital Management (HCM), such as Rippling, tightly integrated, gives companies the data visibility across the organization to better identify trends and root causes to make faster and better decisions to impact efficiency and profitability.
A strong DOP can further link production and operational metrics that may be affected by employee engagement, including:
- Safety Incidents
- Effectivity
- Manufacturing Velocity
- Defect Rates
Characteristics of a manufacturing DOP include adaptability for fast-changing business needs, artificial intelligence (AI)-based for efficiency and innovation and accessibility beyond the browser to streamline both the physical and digital experience for employees, customers, suppliers, and other stakeholders.
While the goal of designing and maintaining a DOP is to have all technology components in place to support the entire business, the path toward that objective can be achieved incrementally. Setting an ultimate desired outcome and determining the appropriate steps in that direction result from collaboration with a manufacturing company’s technology partner. That advisor can help assess existing technology gaps, establish strategic goals, determine a manageable time frame, identify resources and evaluate other factors to create a technology roadmap and execution plan that ultimately achieve a DOP and deliver measurable outcomes.
To learn more about incorporating a DOP approach to affect your employee retention, operational efficiency and profitability, please reach out to your Account Manager or contact us.
Harold Ford, Employee Experience Practice Director at Net at Work, has helped Human Resources (HR) and Payroll departments build strategic value in their organizations since 1994. He has helped thousands of companies throughout North America improve engagement, productivity, and profitability, unleashing the power of their businesses through the digital transformation of HR. He is a member of the Society of Human Resources Management (SHRM) and has earned his SPHR and SHRM-SCP certifications.